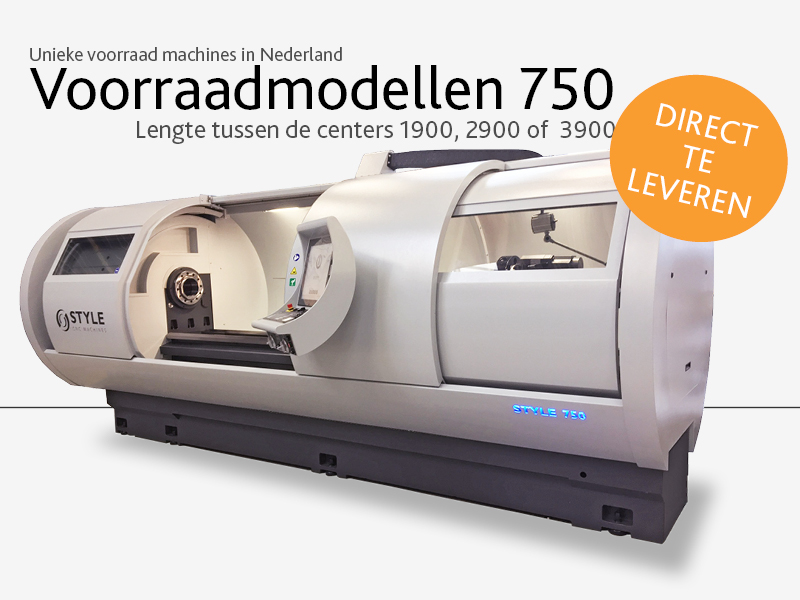
08 Jan R&D developments
Good innovations often arise in practice, based on what customers demand. This also applies to various innovations that the R&D departments are working on every day. Real innovations that many companies can take advantage of.
DEVELOPMENT
R&D DEPARTMENT
Did you know that … Many innovations arise directly from the demand of our customers!
Sizing and printing
One of the innovations in which the customer’s wishes have been carefully listened to is the dimensioning and printing in the STYLE control system. The demand for this position was raised during the TechniShow. Thanks to this customer demand, we were able to take this to a higher level. Drawing is already the heart of the STYLE control, now you can directly add sizes and dimensions to it and even print the drawing from the drawing program.
So you can deliver the workpiece with the corresponding parts – the drawing with the dimensions on it, without having to go back to the work preparation to make the drawing. To guarantee quality, end customers often require that the supplied / produced parts are supplied including a drawing with the dimensions.
Making this drawing in the CNC control avoids duplication. This option offers a good solution for companies that program the machine manually, for example from a sketch. Drawings can also be saved as a reference work. Because no other CNC control offers this option, we have developed this. A unique dimensioning and printing system that provides a significant time saving for every manufacturing company.
STYLE turning dimensioning
STYLE milling dimensioning
Broaching on a CNC lathe
Broaching or pull milling is a technique for inserting and applying one keyway on a STYLE 510. The tool performs a cutting movement to achieve the desired result. The making of keyway slots can be done on a separate broaching machine. As a result of a customer wish to be able to do this directly on his STYLE lathe, our R&D department started working. They have developed an option that makes this operation superfluous and with which keyways can be cut on the STYLE 510 lathe.
A spindle brake is a block brake that blocks the spindle at the desired position. This makes it possible to crumble simple keyhole slots. The material is not loaded by the spindle brake, the process is computer-controlled and very precise.
The spindle brake construction is made up of a clamp system on which a brake disc is mounted. The brake disc is clamped by means of a hydraulic position brake which is controlled by a compact 30 bar hydraulic unit. The system therefore delivers a braking torque of 103 Nm.
Broaching on a STYLE 510 CNC lathe
U-type steady rest
Our R&D department has also developed improved steady rests in consultation with various customers. This question also arose because a customer wanted to save time when clamping heavier and longer products. Two steady rests have been developed, one for the 510 lathe and one for the 750 lathe. A solution was sought to make it easier to open and attach the steady rest. The most important thing was to achieve a larger diameter range. Our R&D department has also developed improved steady rests in consultation with various customers.
The existing steady rest for the 510 lathe had a diameter of 20 – 190 mm and of 150 – 300 mm. This has been reduced to one pair of steady rests with a range of 10 – 300 mm. The existing steady rest of the 750 lathe had a diameter of 50 – 300 mm and 60 – 400 mm. The new steady rest have a diameter of 50 – 530 mm. These steady rests for both the 510 and the 750 lathe are called the U-type steady rests. In addition, the construction is technically improved, which guarantees even more stability.
U-type steady rest STYLE 750
U-type steady rest STYLE 510
U-type steady rest STYLE 750
This is an article from the STYLE magazine – Winter edition